Introduction
Choosing the right PTFE tube extruder is critical for businesses involved in manufacturing high-quality polytetrafluoroethylene (PTFE) tubes, widely used in industries like aerospace, medical, automotive, and chemical processing. PTFE tubes are valued for their exceptional chemical resistance, low friction, and high-temperature tolerance, making the selection of reliable PTFE processing equipment a pivotal decision. A poorly chosen extruder can lead to production inefficiencies, increased costs, and compromised product quality.
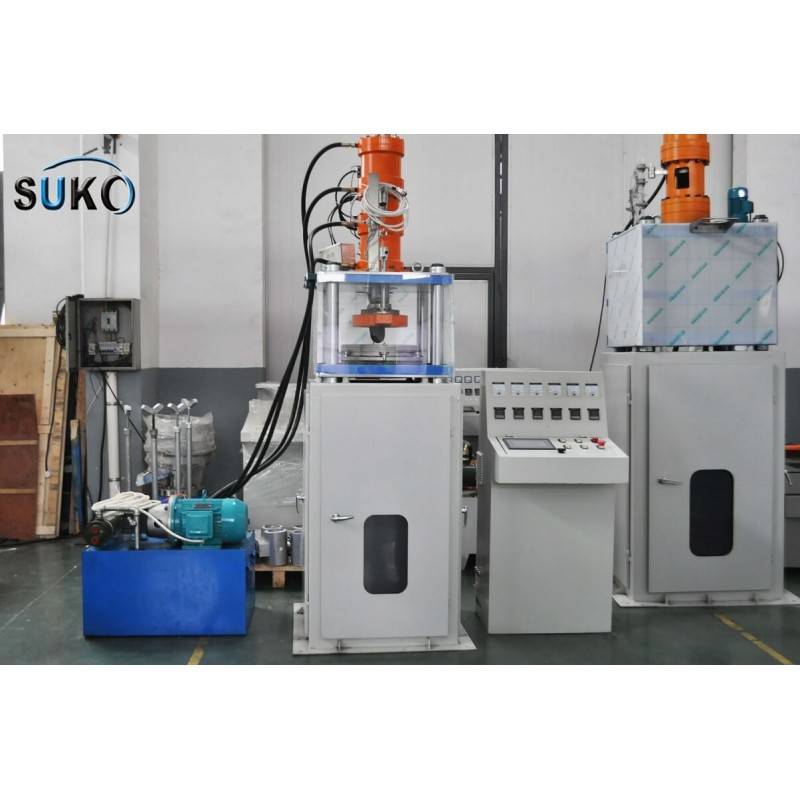
Why Choosing the Right PTFE Tube Extruder Matters
PTFE tubes are integral to applications requiring durability and precision, such as medical catheters, chemical transfer lines, and electrical insulation. The extruder you choose directly impacts:
- Product Quality: Consistent wall thickness, smooth surfaces, and precise diameters.
- Production Efficiency: Faster cycle times and reduced material waste.
- Cost Management: Lower maintenance costs and energy consumption.
- Compliance: Meeting industry standards like ISO 9001 or FDA regulations for medical-grade PTFE.
According to a 2023 report by Grand View Research, the global PTFE market is expected to grow at a CAGR of 4.6% from 2023 to 2030, driven by demand in medical and industrial sectors. This growth underscores the need for high-quality PTFE processing equipment to stay competitive.
Key Factors to Consider When Choosing a PTFE Tube Extruder
To select the right PTFE tube extruder, evaluate the following factors based on your business needs:
1. Production Capacity and Scalability
Your extruder’s output capacity should align with your current and future production goals. Small businesses may need extruders with a capacity of 10–50 kg/hour, while large manufacturers may require 100–500 kg/hour.
Capacity Range | Business Type | Typical Applications |
---|---|---|
10–50 kg/hour | Small-scale | Medical tubing, lab equipment |
50–200 kg/hour | Medium-scale | Automotive, aerospace components |
200–500 kg/hour | Large-scale | Industrial hoses, chemical lines |
Tip: Choose modular PTFE processing equipment that allows upgrades for scalability.
2. Extrusion Technology
PTFE tube extruders use different technologies, such as ram extrusion or paste extrusion, each suited for specific applications:
- Ram Extrusion: Ideal for producing long, continuous tubes with consistent diameters. Best for industrial applications.
- Paste Extrusion: Suitable for thin-walled, flexible tubes used in medical and electrical applications.
Expert Insight: A 2022 study by the Society of Plastics Engineers noted that paste extrusion offers 20% higher precision for thin-walled PTFE tubes compared to ram extrusion.
3. Material Compatibility
Ensure the extruder supports the specific PTFE grades you use, such as virgin PTFE, filled PTFE (e.g., carbon or glass-filled), or custom blends. Compatibility prevents material degradation and ensures product quality.
4. Automation and Control Systems
Modern PTFE tube extruders feature advanced control systems for precision and efficiency. Look for:
- PLC (Programmable Logic Controller): Enables real-time monitoring and adjustments.
- Touchscreen Interfaces: Simplifies operation and reduces training time.
- Data Logging: Tracks performance metrics for quality control.
Statistic: According to a 2024 report by McKinsey, automated manufacturing equipment can reduce production downtime by up to 30%.
5. Energy Efficiency
Energy-efficient extruders lower operational costs and support sustainability goals. Look for features like:
- Variable frequency drives (VFDs) to optimize motor performance.
- Insulated heating zones to minimize heat loss.
Example: A leading PTFE extruder manufacturer reported that their energy-efficient models reduced power consumption by 15% compared to traditional systems.
6. Maintenance and Support
Choose a supplier offering robust after-sales support, including:
- Spare parts availability.
- On-site or remote technical support.
- Comprehensive training programs.
Trustworthy Source: ISO 9001-certified manufacturers, such as those listed by the Plastics Industry Association, ensure reliable equipment and support.
7. Cost vs. Value
While budget is a factor, prioritize long-term value over upfront cost. A high-quality PTFE tube extruder with advanced features may have a higher initial cost but offers better ROI through efficiency and durability.
Comparing Top PTFE Tube Extruder Brands
To help you narrow down options, here’s a comparison of leading PTFE processing equipment brands based on key metrics:
Brand | Technology | Capacity (kg/hour) | Automation Level | Energy Efficiency | Warranty |
---|---|---|---|---|---|
Bausano & Figli S.p.A. | Paste Extrusion | 10–100 | High (PLC, touchscreen) | VFD, insulated zones | 2 years |
Davis-Standard, LLC | Ram Extrusion | 50–300 | Medium (basic PLC) | Standard | 1 year |
KraussMaffei Group | Hybrid | 20–500 | High (data logging) | Advanced VFD | 3 years |
Note: Always request a demo or trial to assess equipment performance in your production environment.
How to Evaluate Suppliers of PTFE Tube Extruders
Selecting a reliable supplier is as important as choosing the right equipment. Follow these steps:
- Verify Credentials: Check for certifications like ISO 9001 or CE marking.
- Review Case Studies: Request case studies or testimonials from similar industries.
- Assess Customization Options: Ensure the supplier can tailor the extruder to your specifications.
- Compare Lead Times: Confirm delivery schedules to avoid production delays.
- Evaluate Support Services: Prioritize suppliers with global support networks.
Authoritative Reference: The International Association of Plastics Distribution (IAPD) recommends partnering with suppliers who provide transparent documentation and proven track records.
Common Mistakes to Avoid
- Ignoring Scalability: Choosing an extruder without future-proofing limits growth.
- Overlooking Training Needs: Inadequate operator training leads to errors and downtime.
- Focusing Solely on Price: Low-cost extruders may compromise quality and reliability.
- Neglecting Maintenance Plans: Skipping regular maintenance increases repair costs.
FAQ Section
1. What is the difference between ram and paste extrusion for PTFE tubes?
Ram extrusion is suited for continuous, large-diameter tubes, while paste extrusion is ideal for thin-walled, flexible tubes used in medical or electrical applications. Paste extrusion offers higher precision for smaller sizes.
2. How do I know if a PTFE tube extruder is energy-efficient?
Look for features like variable frequency drives (VFDs), insulated heating zones, and energy consumption data from the manufacturer. Request a performance report to verify efficiency claims.
3. Can I use the same PTFE tube extruder for different PTFE grades?
Yes, but ensure the extruder is compatible with virgin, filled, or blended PTFE. Consult the supplier to confirm material compatibility and avoid processing issues.
Conclusion
Selecting the right PTFE tube extruder is a strategic decision that impacts your business’s efficiency, product quality, and profitability. By focusing on production capacity, technology, automation, and supplier reliability, you can invest in PTFE processing equipment that meets your needs today and supports growth tomorrow. Avoid common pitfalls, leverage data-driven insights, and partner with trusted suppliers to ensure success.
Ready to elevate your PTFE tube production? Contact our team for expert guidance and a tailored quote on top-tier PTFE tube extruders. Don’t miss out—request your free consultation now!